Business Challenges
- Lacked a mature CAM solution tailored to automate wire harness manufacturing effectively.
- Transitioned from a competing CAD solution to Siemens NX for better functionality and integration.
- Needed a workflow to place wires on 3D surfaces in CAD and convert data into G-Code for their motion platform.
Keys to Success
- Developing a digital twin for simulation and toolpath planning.
- Creating a tool for designing complex wiring harnesses efficiently.
- Choosing Siemens NX CAM and Multi-Axis Deposition for additive manufacturing needs.
- Strong partnership with Emixa for training, support, and technical development, ensuring rapid progress and commercial confidence.
Results
- Cut cycle time by 50%.
- Reduced assembly time from four months to three weeks.
- Reduced design and redesign time of wiring looms by over 70%.
- Won three new clients and achieved significant time savings in various processes.
Driving Efficiency in Wire Harness Manufacturing
Q5D is pioneering the full automation of wire harness manufacture. Their robots and software translate designs into products digitally retaining established components wherever possible. Their automated systems route, protect and terminate wires to create complete wiring harnesses. The wiring can be integrated onto almost any 3D surface or laid out as a separate component. Minimal fixturing means very high design flexibility. The result is precise and repeatable, reduces labour by 80% or more and massively reduces factory footprint. This lowers cost, shortens supply chains and improves quality.
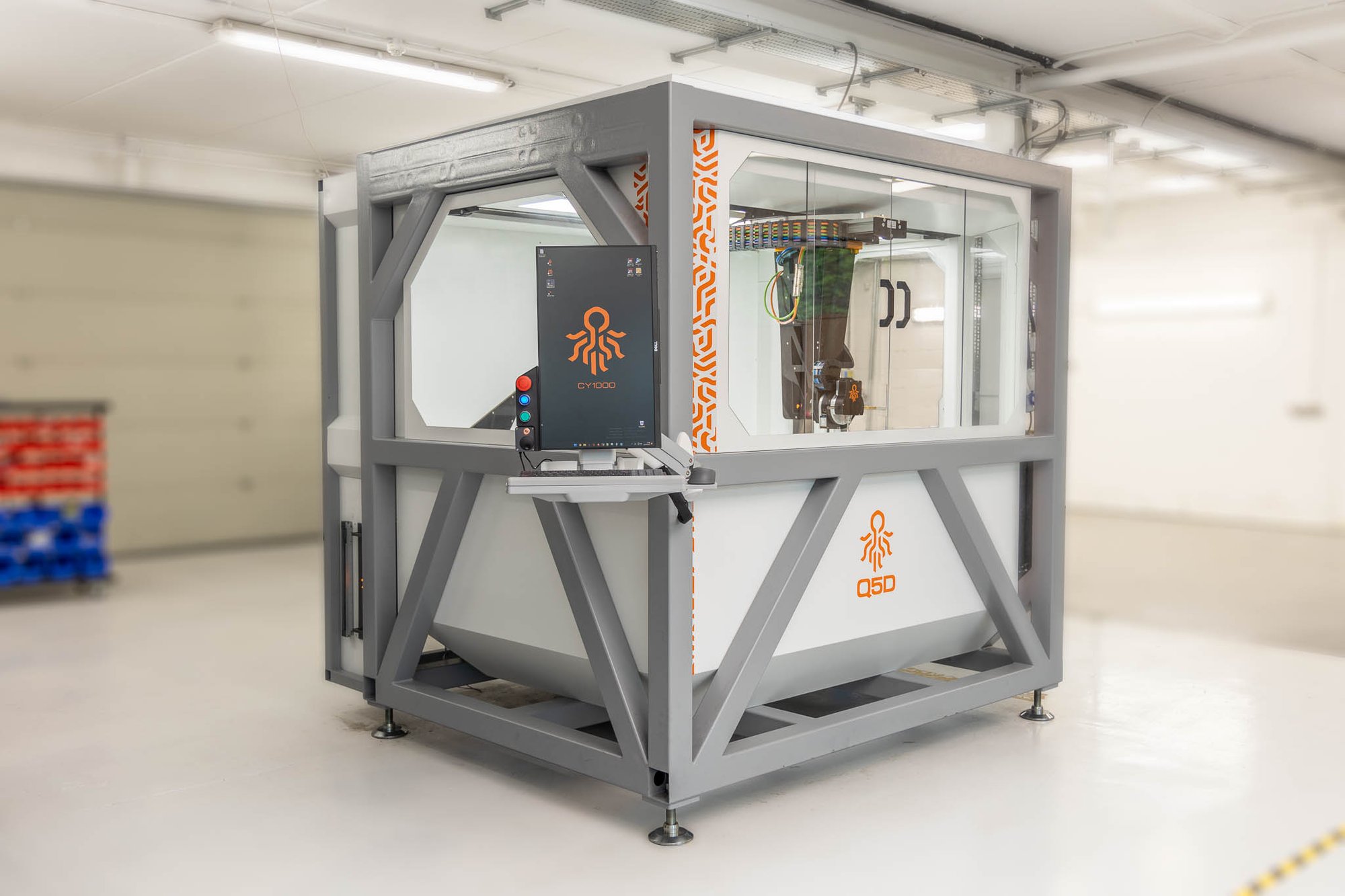
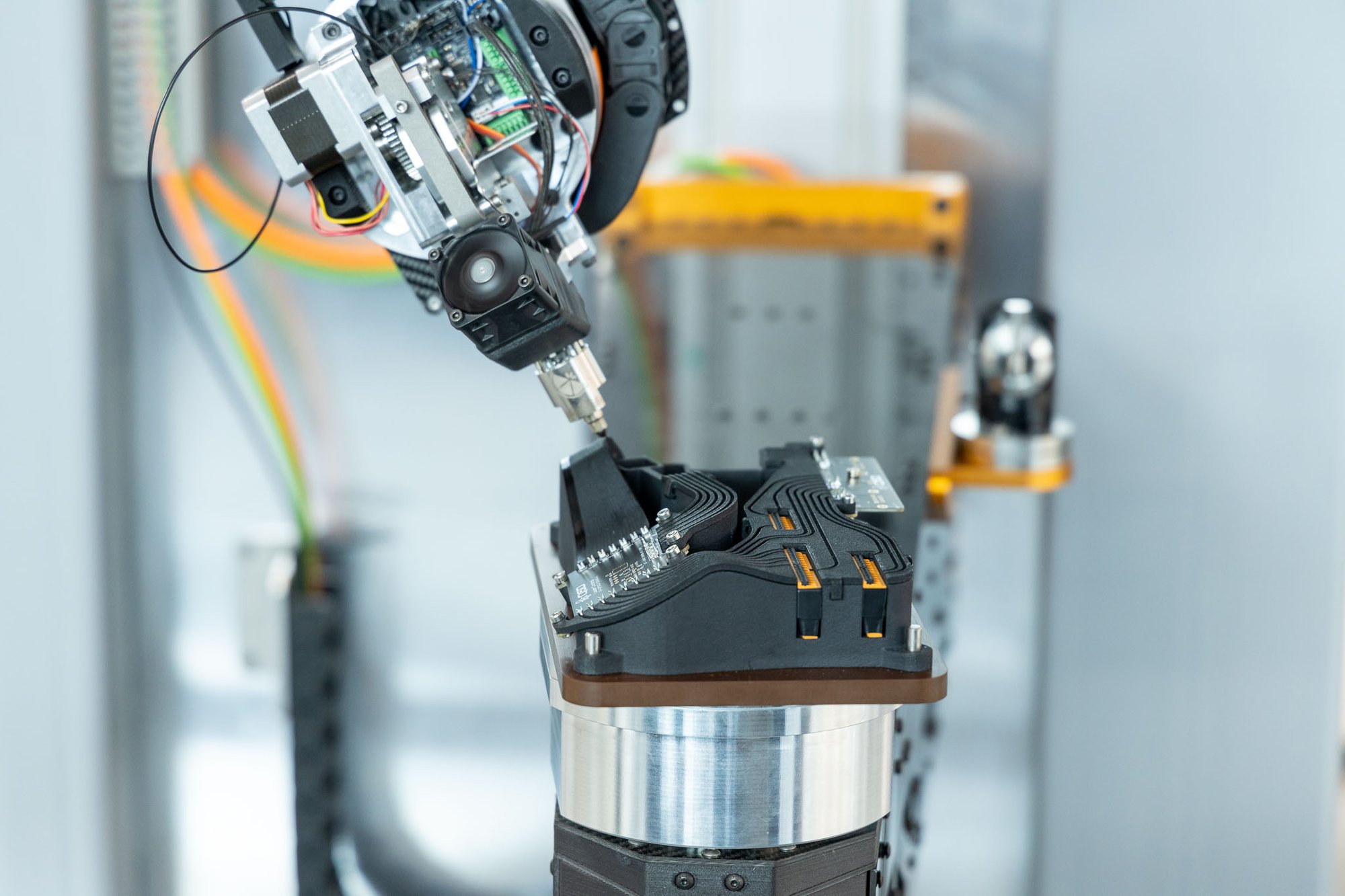
Business Challenges
Q5D faced challenges in automating wire harness manufacturing, particularly needing a workflow to place wires onto a 3D surface in CAD and convert this data into G-Code for their motion platform. They trialed various CAM solutions and found Siemens NX CAM and multi-axis deposition as the most mature options for their needs. This decision also led to transitioning from a competing CAD solution entirely into Siemens NX.
Keys to Success
The partnership between Q5D and Emixa has been instrumental in driving innovation and efficiency in wire harness manufacturing. A key success factor was the adoption of Siemens NX CAM and multi-axis deposition, which provided advanced toolpath programming functions for additive manufacturing. This transition enabled Q5D to replace a competing CAD solution and streamline operations effectively.
Emixa’s support was critical in this journey. Their collaboration helped Q5D create a digital twin of their machine, aiding in simulation and toolpath planning. The development of a bespoke CAD tool allowed for rapid and accurate design of complex wiring harnesses across 3D surfaces, significantly enhancing productivity. This seamless integration of software and hardware has positioned Q5D to deliver high-value projects efficiently and grow their market presence.
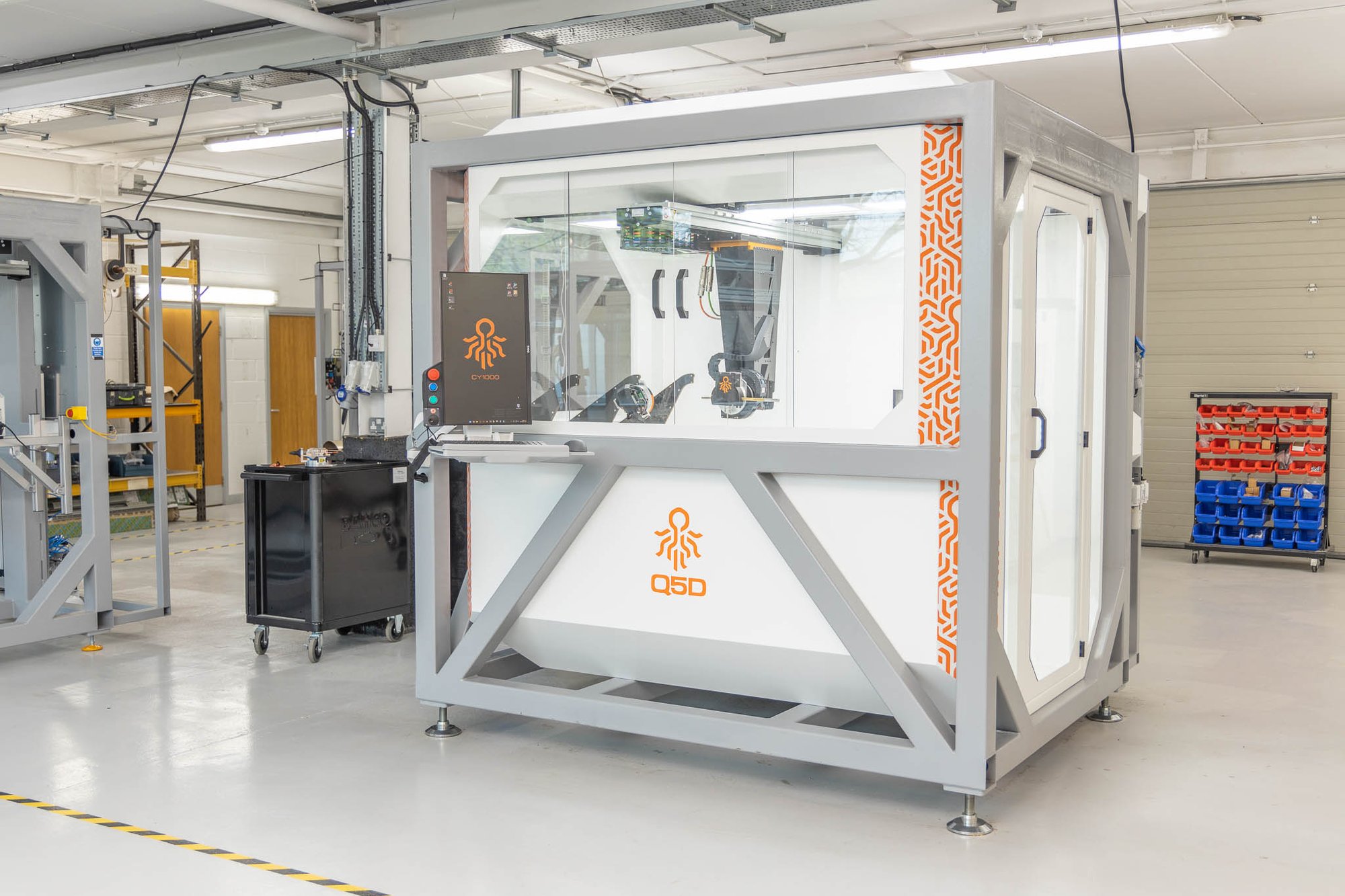
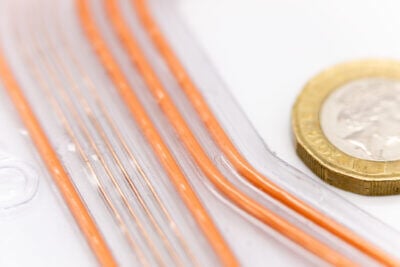
Results
Q5D has achieved remarkable results through the integration of Siemens software, demonstrating tangible improvements across their operations. Assembly times have been reduced from four months to just three weeks, while design and redesign times for wiring looms have decreased by more than 70%. These efficiencies have enabled Q5D to cut cycle times by 50% and save 60% in model preparation time.
These operational advancements have translated into commercial success. Q5D has won three new clients and built a reputation for delivering high-quality, innovative solutions quickly. The Siemens software environment has provided Q5D with the tools to prove the value of their unique technology, streamline workflows, and support their growth trajectory. With the continued backing of Emixa and Siemens, Q5D is well-positioned for sustained success and industry leadership.
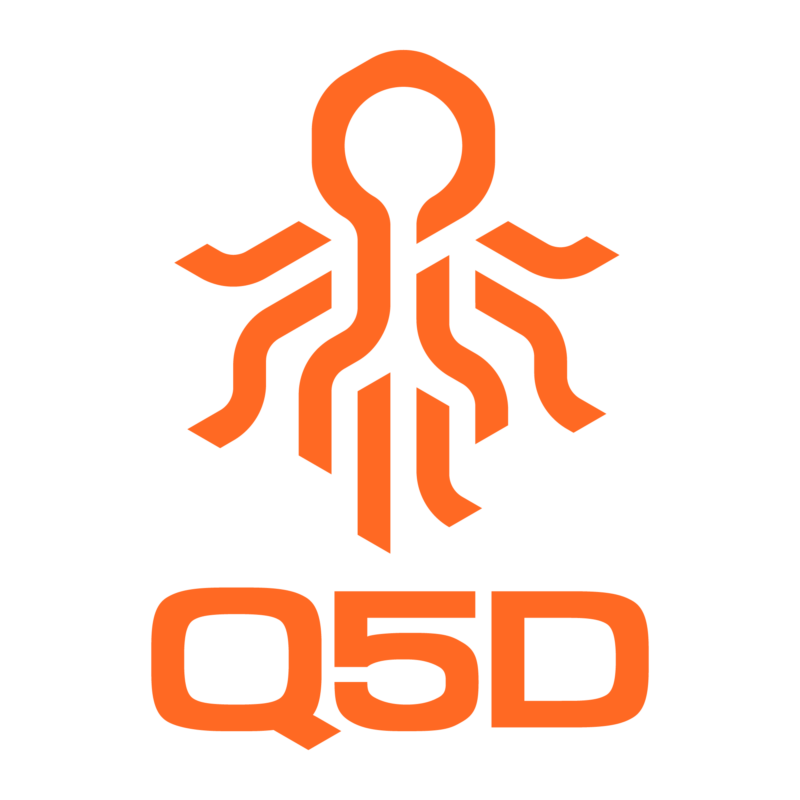
Siemens software has cut design and redesign time of wiring looms by more than 70%
Using Siemens CAD CAM and file sharing tools we have been able to quickly design, manage and deliver a broad range of capital products and demonstration parts which can be manufactured using our unique products. With the help of Emixa and the power and harmonious digital environment provided by Siemens software our start-up hardware technology company is now customer rich and moving quickly on a path to success - appreciated very much by our investors and ensuring continued growth.
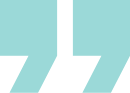
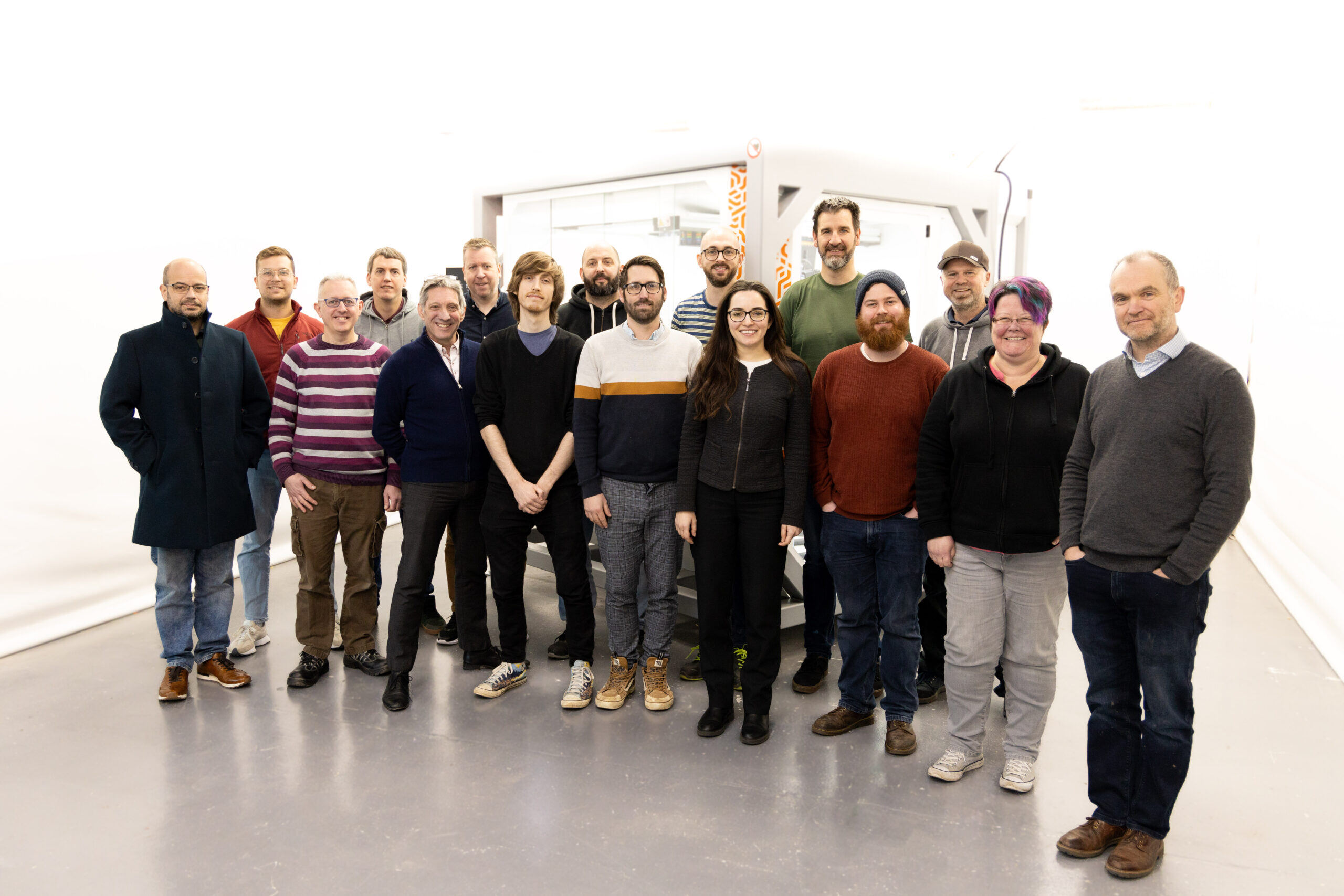
Peter Todd
Marketing Lead, Q5D
Related Cases
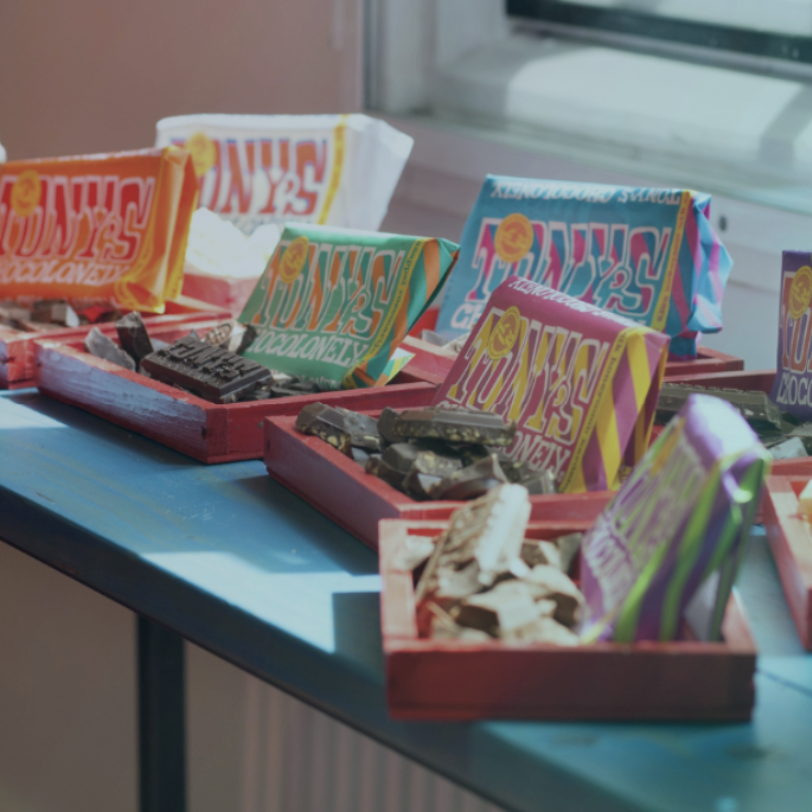
Tony's Chocolonely
The Dutch Tony's Chocolonely has a mission: to free the chocolate industry from slave and child labour. The company works together with thousands of cocoa farmers and dozens of suppliers. To make that chain work together more efficiently, faster and cheaper, Emixa used Boomi to ensure that the many software systems of the company were integrated.
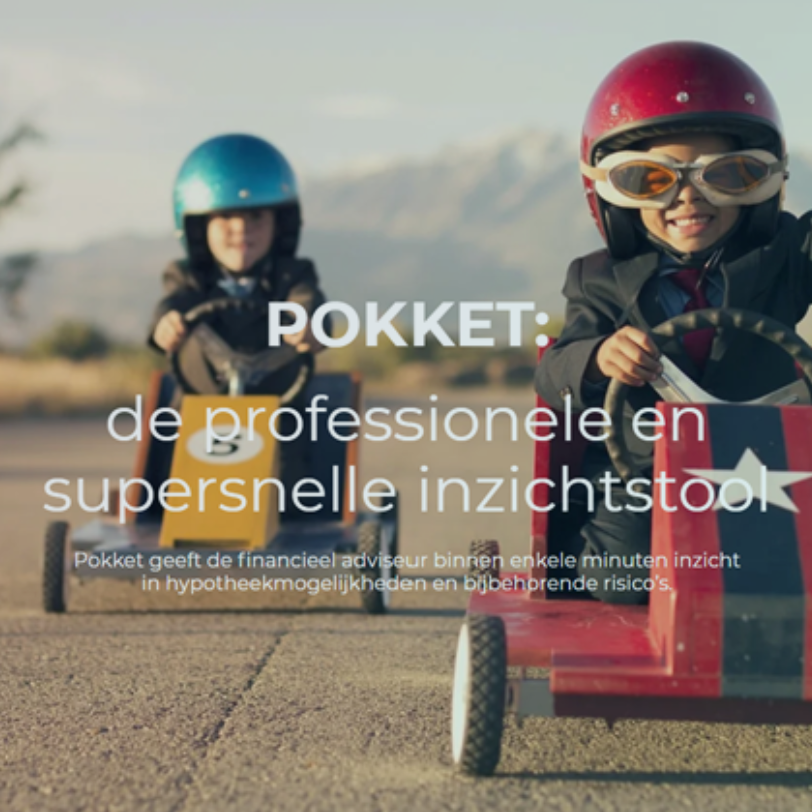
Pokket
Pokket is an online tool designed to provide financial advisers with rapid insights into mortgage options and associated risks. Apart from fast analysis, the application generates instant reports that can be shared with customers on the spot. This not only reduces advisory call durations by 75%, but also enables advisers to increase their revenue by 10%, as they can dedicate more time to offering personalised attention to customers.
%2015%25.png)
Secrid
Secrid designs and sells innovative wallets all over the world and collaborates with more than fifty suppliers. To make that entire chain work together more efficiently, faster and cheaper, Emixa built a completely new supplier portal with low-code technology from Mendix and integrated the systems with Boomi.