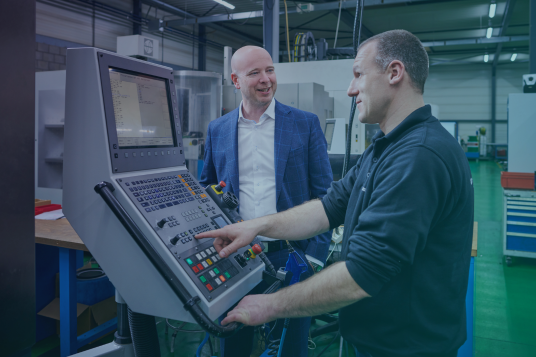
Case study Mevi Group
Mevi, with a legacy spanning over 50 years, specialises in designing, developing, and manufacturing parts, modules, and machines.
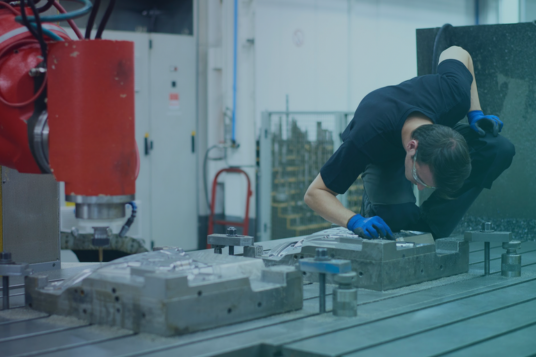
Case study Surtechno
Mould service company Surtechno plays a pivotal role for European car manufacturers.With 35 employees, the Surtechno modifies, repairs, and refines moulds for producing large plastic components, serving clients like Audi, BMW, Mercedes, Opel, and Porsche.
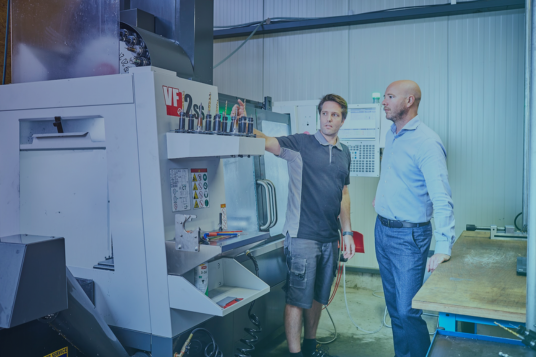
YouniQ Machining: Achieving Precision and Efficiency through Innovative Manufacturing Solutions
With only two employees, the entire process at YouniQ is software-driven.This enables fast, cost-effective production without human errors.
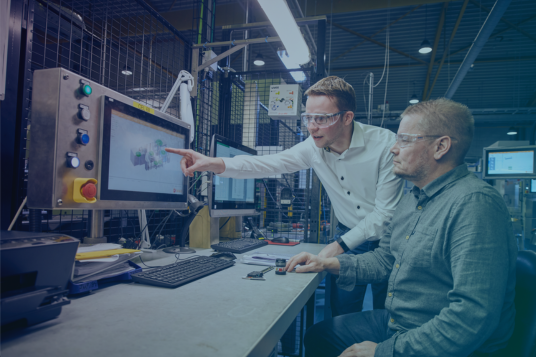
Case study Oerlikon Eldim
Oerlikon Eldim (NL) B.V.manufactures and processes components for aircraft engines, meeting stringent quality standards.
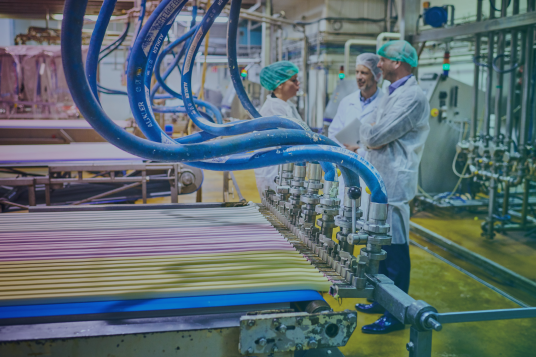
Case study Mr. Mallo
The Mr.Mallo group, a modest player in the sweets industry but a powerhouse in marshmallow production, has been leading the European market since 1907.
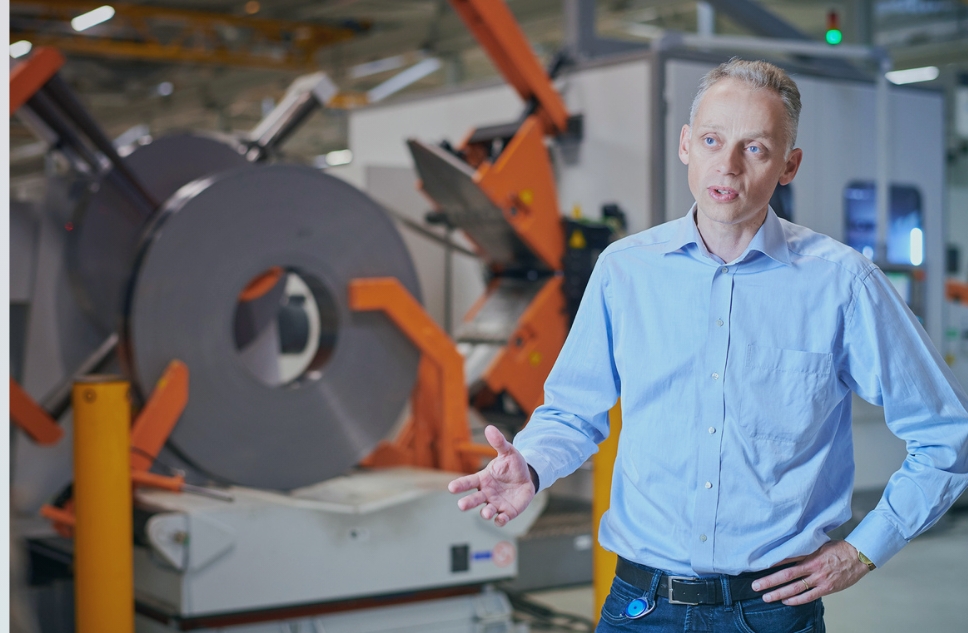
Case study ART Group
ART Group functions as a comprehensive provider of product creation processes, covering the entire spectrum from the initial conceptualization phase to the mass production stage, and everything in between.
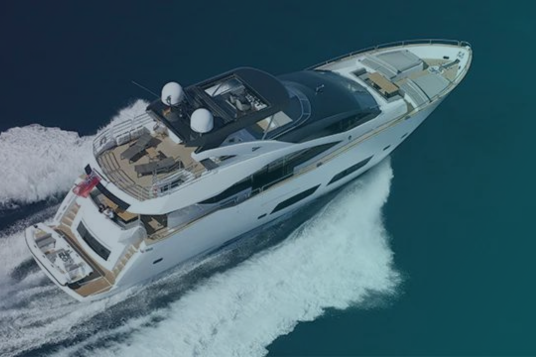
Case study Sunseeker
A global leader in the design and build of luxury motor yachts, Sunseeker International exports 99 percent of its product range and employs over 1,800 highly trained staff in the company’s shipyards on Britain’s South Coast.
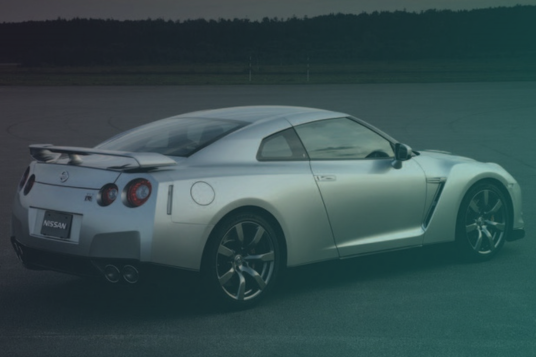
Case study Nissan
In Nissan's pursuit of sustainable mobility and competitiveness in the automotive industry, the V-3P program, powered by Siemens PLM technology, has delivered outstanding results.
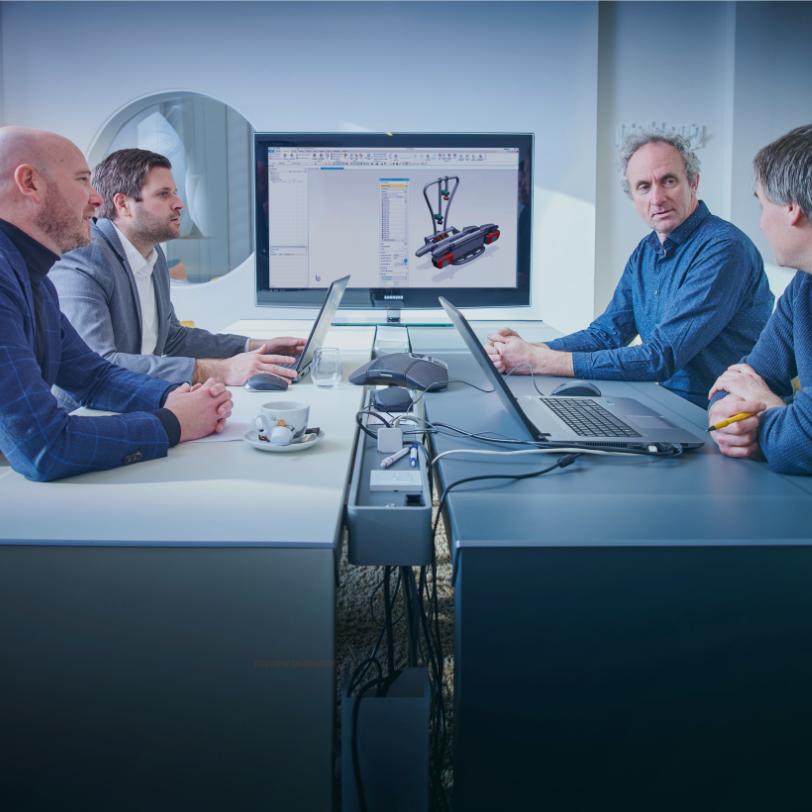
NTS Transforms Global Operations with Digital Innovation Solutions
NTS specialises in developing, manufacturing, assembling, and testing complex (opto)mechanical systems and modules for leading high-tech machine builders.