Solid Edge Training Insights from Our Expert
Last edited on Feb, 13 2025 02:54:22 PM
Reading time: 3 minutes
Written by Phoebe Costello
Table of contents
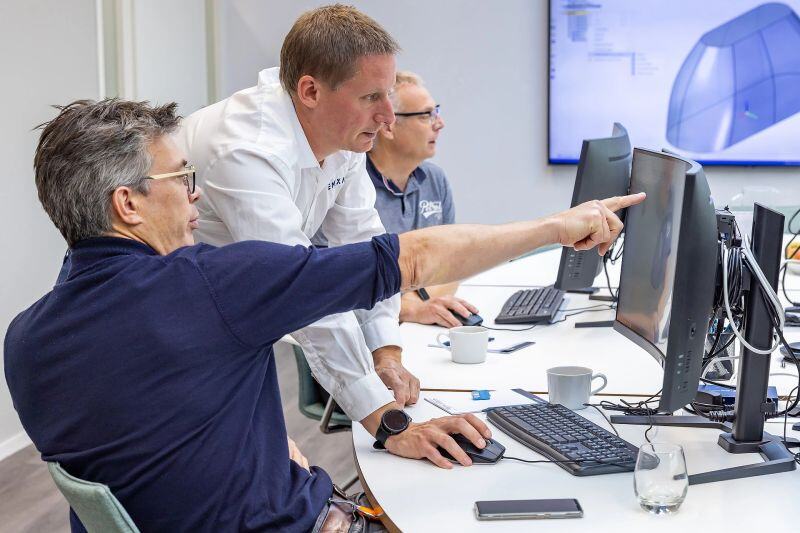
Reduce modelling time from 10 clicks down to 4 with expert training. In this blog post, hear from our Design Consultant, Christopher Morgan on why software training is essential for saving your resources.
Technical Expertise
Q: What is your role at Emixa and how long have you worked here?
A: My role is Principal Design Consultant for Solid Edge, I look after training, pre-sales and everything Solid Edge. I started with the company in January 2018.
Q: How long have you worked with Solid Edge?
A: I began using Solid Edge in 2007. I started on version 20 and then soon moved to ST, which was ST1, the first one that had synchronous technology.
Q: Are you experienced in other CAD systems?
A: I started my career using CATIA at university. The companies I've worked for had Inventor and Solidworks. I'm proficient at Fusion and Solidworks. I also know NX as well, which is another product that we sell CAD-wise.
Solid Edge in Practice
Q: In your opinion, what makes Solid Edge stand out from other CAD systems you've used in the past?
A: Definitely synchronous technology. I find it works on low-spec workstations much better than other CAD systems, so if you're a smaller company who can't afford a high-spec workstation, Solid Edge will still work well.
Q: What industry & applications have you worked with using Solid Edge?
A: The first industry I used Solid Edge was retail shelving and fridges. The second industry was oil and gas, I specialised in high pressure injection of methanol into lines that had taken oil out of oil wells. The third industry was general engineering and access equipment. I worked for a small company that made access equipment for companies like JLR and Eurostar.
Q: In your opinion, what is your favourite feature of Solid Edge?
A: My favourite feature is the flexibility to work in both history-based and synchronous modelling. Synchronous modelling allows us to treat the model like it's a model rather than just sketches. It allows us to work in a truly holistic way.
Training Methods
Q: How do you structure your training sessions for beginners versus advanced users of Solid Edge?
A: For beginners, I will do it dynamically. If they're struggling with sketching, I will spend more time making sure they understand it. I find that doing training on-site or in the Emixa office for a basic training is a must. Doing that remotely is not as efficient. Students get twice as much out of it if it’s in-person because we as trainers can be over their shoulder, see where they are going wrong and help them.
With the advanced users, you're just showing more advanced commands. Students know the software and your job is to expand the commands they know. It’s always positive when we can improve a student's CAD flexibility and functionality.
Q: What's the most effective way of training, remote, on-site, or in our Emixa office?
A: Students always get a lot more out of the training when they're in our Emixa office. We're set-up, we've got the correct hardware, we've got the correct licenses, and it means that everything is ready to use. I would say remote is the least productive. On-site is good but there is distractions, emails coming in, Teams’ calls, or team members coming in and knocking on the door.
Q: How do you balance theoretical instruction with hands-on learning in your sessions?
A: During my sessions, I always start with theoretical, but I find 95% of our users prefer as much hands-on as possible. So often I will use the theoretical slides that we have as a guide to make sure I don't miss anything, but everything will be done in the CAD software.
Q: How do you assess whether students have successfully grasped the concepts you've taught?
A: If we do a multi-day course, on the start of the second, third and the fourth day, I’ll do a refresh of what we did on the day before. For the first half hour we have a project where we look at what we've done. On the first day, students struggle. On the second day, they've slept on it, the knowledge has settled and then they find it easier and it gets better with each day. It gives me an idea if we’ve done everything correctly on the first day, if I give them an example to go and recreate some sketches to draw and they do it well, I can assess that. If they're struggling, then the first day didn't go right, so I'll spend another hour making sure that they're up to speed.
Q: Can you share an example of a difficult concept in Solid Edge that student's often struggle with and how do you help them overcome it?
A: Solid Edge has got 2D sketching and the concept of 3D sketching, meaning you can sketch and go in any direction, you can snap to any key point. Some people struggle with that because they create a line, and they spin the model around and it just goes in a completely different direction to what they thought they had created. So teaching them to work in a proper 3D environment, lock the line to a plane, lock the line to a direction, make sure it's going upwards or left or right or down on each plane. This is used for Geometric parts and once they get the hang of that, you can see it clicks in their eyes and now they've gone from struggling to feeling confident with that in a short time span.
Q: As an experienced design engineer and a trainer, how important do you think training is in getting the most out of the software?
A: Yesterday, I did a course and I learned something new on the software. I find that even myself, I'll go and try a keyboard shortcut, I'll do something slightly different, and I will learn it. I think it's really important that users have refresher courses every year to make sure they are getting the most out of the software.
We do something called a ‘design review’ where we go to our customers, have a look at their models, the way they’re working, watch them design, ask them to go and create some parts and then we review those. I'd say, pretty much 100% of time, there will be something on the model that they could do faster, that they could reduce from ten clicks down to 4 clicks.
People get set in their ways; they develop bad habits. They've got certain products, and they design in a specific way, they use specific tools. It’s incredibly valuable to refresh their knowledge, help them to use more commands and save their time.
Student Needs
Q: How do you adjust your training when working with teams who have varying levels of experience?
A: For the people that are more experienced, I will give them their own project while I look after people that need a more support. I did a surfacing course for a company that produces buses, and I had six in a team. Two were going off doing their own thing. Every time, they started doing things on their own, I’d give them another bit of a challenge and I would check on them.
The other people that were less-experienced would do the core activities, so it's always good to have extra projects on every course for the people that are quicker and feel more confident. For an everyday course, we might have five modules and they'll be a sixth one which will be projects, and these projects are for the more advanced people.
Q: Can you describe a time when you had to modify your training approach based on feedback?
A: I'd say every six months we review the courses. So quite often, especially if it's a customer that does a certain product and the example that we're doing is completely irrelevant, I will go and find an appropriate data set and make sure that that is relevant.
A lot of our courses will cover sheet metal, plastic injection moulded parts, machine parts. If you've got a customer that only does vacuum forming, it's pointless doing a lot of these other items. I always try and make sure our four-day course has got enough activities to do for six days. Obviously we've got a set course if we have loads of different customers from different industries, but if I do a course for a customer that's got just one industry area, I will customise it just for that one. I know what that customer makes, I visualise it and the customers appreciate it because I'm designing something for them and they can see when things go wrong and see how I fix it in Solid Edge.
Find the Right Training Course
Investing in professional Solid Edge training is essential to fully leverage the capabilities of your Siemens software. Explore our full range of Solid Edge training courses and find out which is best for you here.
Last edited on Feb, 13 2025 02:54:22 PM
Reading time: 3 minutes
Written by Phoebe Costello
Also see..
OverviewEmixa and WSR continue technical partnership for BTCC 2024
The partnership leverages Emixa's expertise in Siemens Digital Industries Software to enhance...
Read more ⟶How Can Construction Companies Adopt New and Innovative Technologies?
Innovative technologies have the potential to help the construction and infrastructure sectors...
Read more ⟶The True Impact of Siemens Teamcenter Implementation
One of our customers, AAE is an advanced high-tech manufacturer that designs and produces solutions...
Read more ⟶