What is Overall Equipment Effectiveness (OEE)?
Last edited on Jun, 27 2025 02:32:09 PM
Reading time: 12 minutes
Written by Roel Kucukbiyik
Table of contents
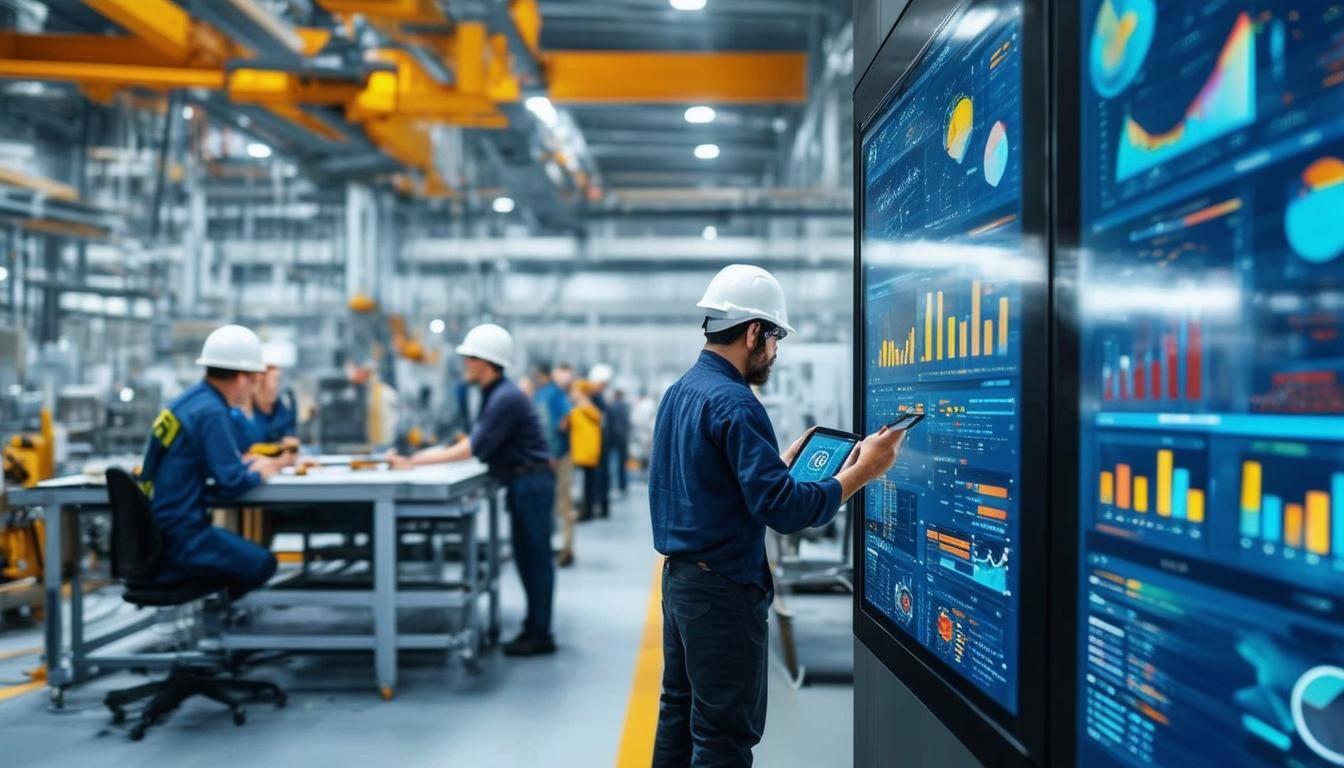
In the world of manufacturing, performance matters. Businesses are under pressure to produce more, faster, and with fewer resources - while keeping costs low and quality high. To do this, they must understand how well their equipment is actually performing. That’s where Overall Equipment Effectiveness (OEE) comes in.
What is OEE (Overall Equipment Effectiveness)?
Overall Equipment Effectiveness (OEE) is a globally recognised metric used to measure the productivity of manufacturing equipment. It combines three critical components - Availability, Performance, and Quality—into a single percentage that reflects how effectively a machine or production line is operating.
A perfect OEE score is 100%, meaning you’re manufacturing only good parts, as fast as possible, with no downtime. While rare, this benchmark helps businesses identify exactly where productivity is being lost and how to recover it.
Who benefits from using OEE?
OEE is particularly valuable for manufacturers of all types—discrete, process, or batch—and is essential for operations, plant managers, and continuous improvement teams looking to:
- Maximise asset utilisation
- Identify and reduce bottlenecks
- Justify investments in new equipment
- Improve maintenance planning
- Measure the success of lean initiatives
At Emixa, we support organisations in capturing OEE data through MES, IoT sensors, and digital twin technologies, then turning that data into actionable improvements.
When should you start measuring OEE?
If your plant struggles with unplanned downtime, inconsistent output, or slow cycle times, now is the time to start tracking OEE. It’s particularly useful:
- During a digital transformation initiative
- When implementing a Manufacturing Execution System (MES)
- As part of lean manufacturing or continuous improvement programs
- Before investing in new machinery or automation
Even if you’re not aiming for 100%, tracking OEE provides a baseline to improve from—and a framework to monitor progress over time.
Where does OEE fit into your manufacturing strategy?
OEE should sit at the heart of your performance improvement strategy. By analysing Availability, Performance, and Quality, you can pinpoint where to focus:
- Availability tracks unplanned and planned stops
- Performance monitors speed losses and small stops
- Quality accounts for rejected parts or rework
OEE can be visualised through dashboards in systems like Opcenter Execution, giving teams real-time insight into shopfloor performance.
Why is OEE more effective than other metrics?
Unlike basic KPIs such as output per hour or defect rate, OEE gives a comprehensive view of production health in a single number. It lets you:
- Quantify productivity losses in exact percentages
- Prioritise areas with the biggest improvement potential
- Benchmark machines, shifts, or plants across your network
- Align production KPIs with broader business goals
OEE can also be automated using IoT platforms, reducing manual data entry and improving accuracy.
What are real-world examples of using OEE?
Here are just a few practical ways manufacturers use OEE:
- Improving maintenance: Identify frequent downtime causes and schedule predictive maintenance
- Optimising shifts: Compare performance across teams to identify best practices
- Justifying investment: Show ROI for machine upgrades with historical OEE data
- Reducing waste: Track scrap and rework to uncover quality issues
At Emixa, we’ve helped clients improve their OEE scores by integrating Siemens Xcelerator technologies like Teamcenter, Mendix, and Opcenter, giving them full control and visibility.
OEE is a powerful metric that gives manufacturers a clear picture of how efficiently their equipment is performing. By breaking down productivity into measurable components, it empowers businesses to reduce waste, increase throughput, and enhance quality - all without additional investment in machinery.
With the right tools in place - like MES, IoT integration, and advanced analytics - OEE becomes more than a metric. It becomes the foundation for smarter, faster, and more sustainable manufacturing.
Frequently asked questions on OEE optimisation
You can increase availability by minimising unplanned downtime through preventive maintenance and quick troubleshooting. Improve performance by optimising the production line, reducing micro-stops and fine-tuning machine settings. Improve quality by identifying and eliminating production errors and performing consistent quality checks.
Consider implementing an OEE monitoring system to quickly identify and resolve problems. Ensure good communication between departments and involve the whole team in improvement initiatives. Standardise measurement methods and collect reliable data for accurate analysis. By consistently working on these aspects, you will improve OEE.
By multiplying these three components, you get the OEE score as a percentage.
For example: if Availability is 87.5%, Performance 83.3% and Quality 93.75%, the OEE is 0.875 x 0.833 x 0.9375 ≈ 54.4%
It is not just a technical yardstick, but a compass that helps you reduce waste, increase machine availability and optimise the quality of your products. By viewing OEE as a dynamic improvement tool, you can work in a structured way to strengthen your operational excellence.
Last edited on Jun, 27 2025 02:32:09 PM
Reading time: 12 minutes
Written by Roel Kucukbiyik
Also see..
OverviewWhat is the Industrial Internet of Things (IIoT)?
The manufacturing and industrial sectors are experiencing a rapid digital transformation. As...
Read more ⟶What is LEAN Manufacturing?
Lean manufacturing, also known as lean production, is a method of making production processes more...
Read more ⟶The Digital Shopfloor Scan: Uncover Operational Improvements
The manufacturing industry is under increasing pressure to operate more efficiently, flexibly and...
Read more ⟶