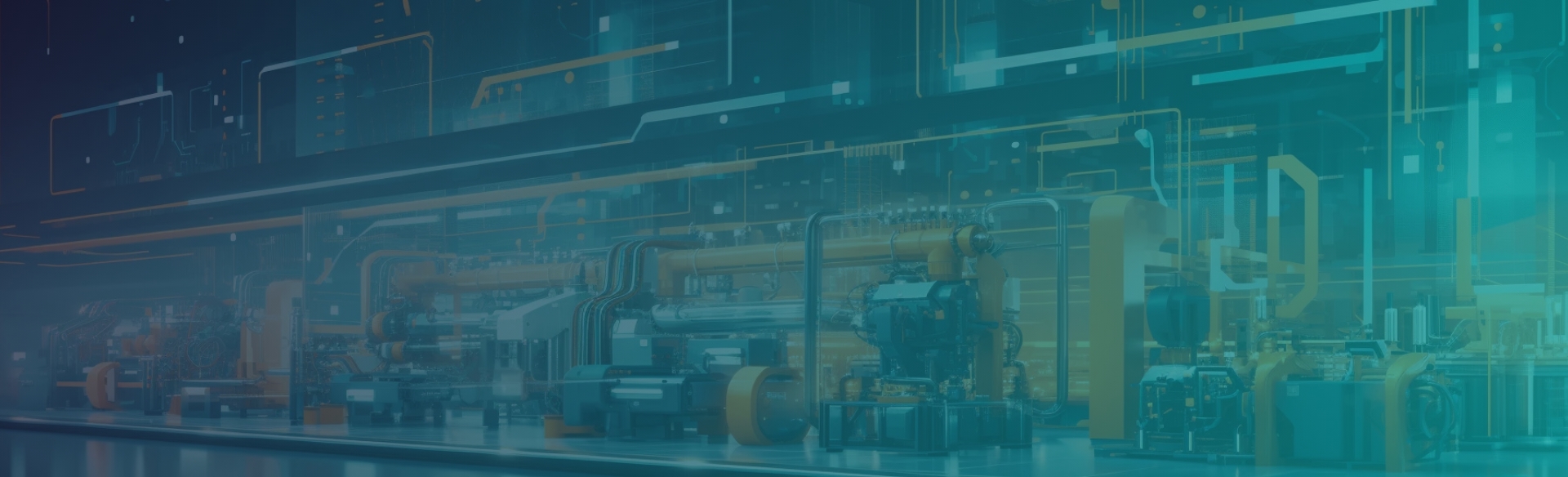
Revolutionising Manufacturing: Forge a Future-ready Industry
Emixa and Mendix provide solutions to help manufacturing companies optimise their business operations and take full advantage of digital transformation. Discover our comprehensive manufacturing menu.
Manufacturing Menu
Do you want to work with Mendix to move optimally and flexibly with current developments? Then it is advisable to view Mendix from a broad perspective and determine whether and how the technology can become a permanent part of your IT architecture. In this way, instead of just a 'point solution' (a solution for one specific pain point), it becomes a basis for working faster, smarter and more efficiently across the board. To get the most out of Mendix and to give you an overview of the possibilities, Emixa has put together a special manufacturing menu for production companies. Time to take a closer look.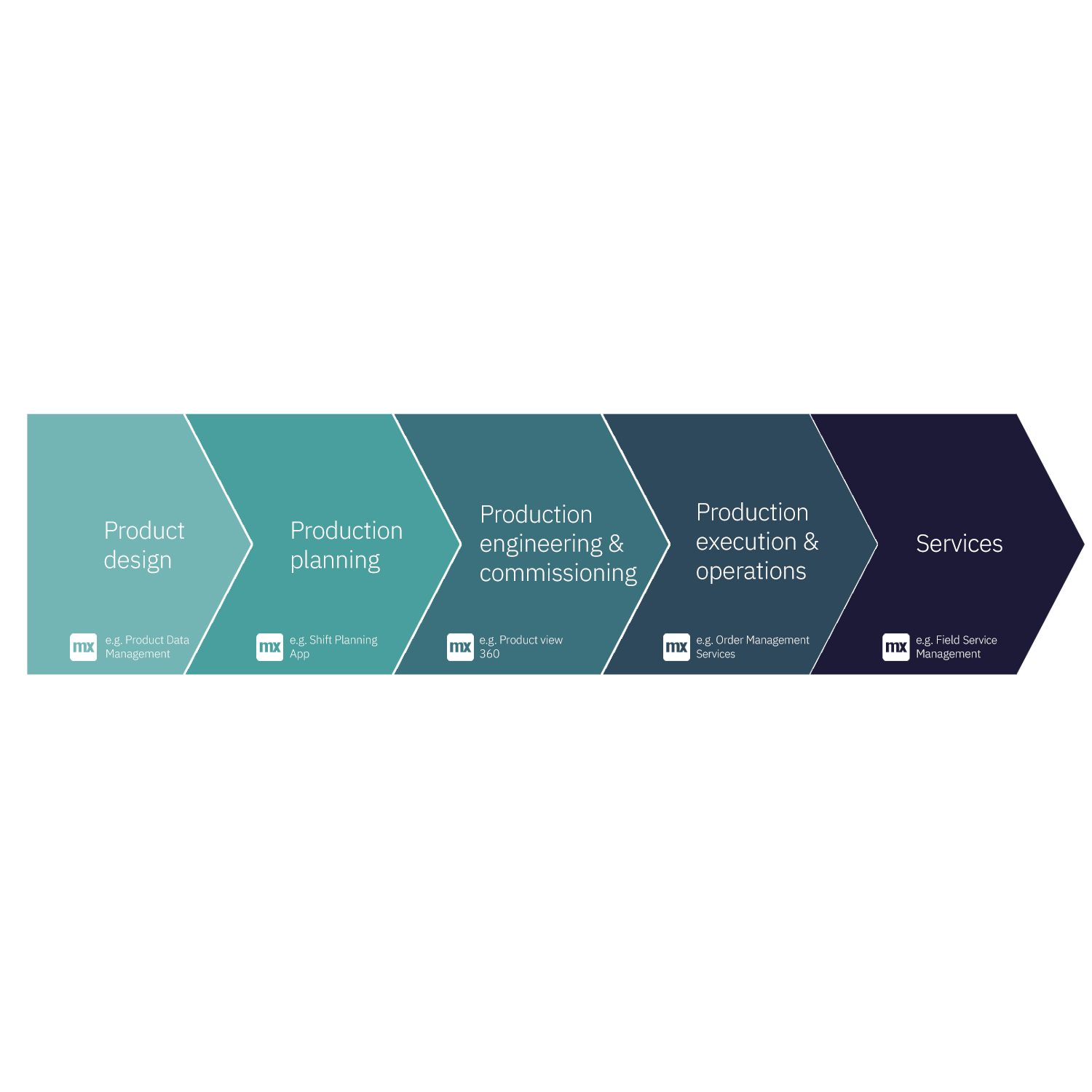
Manufacturing Menu
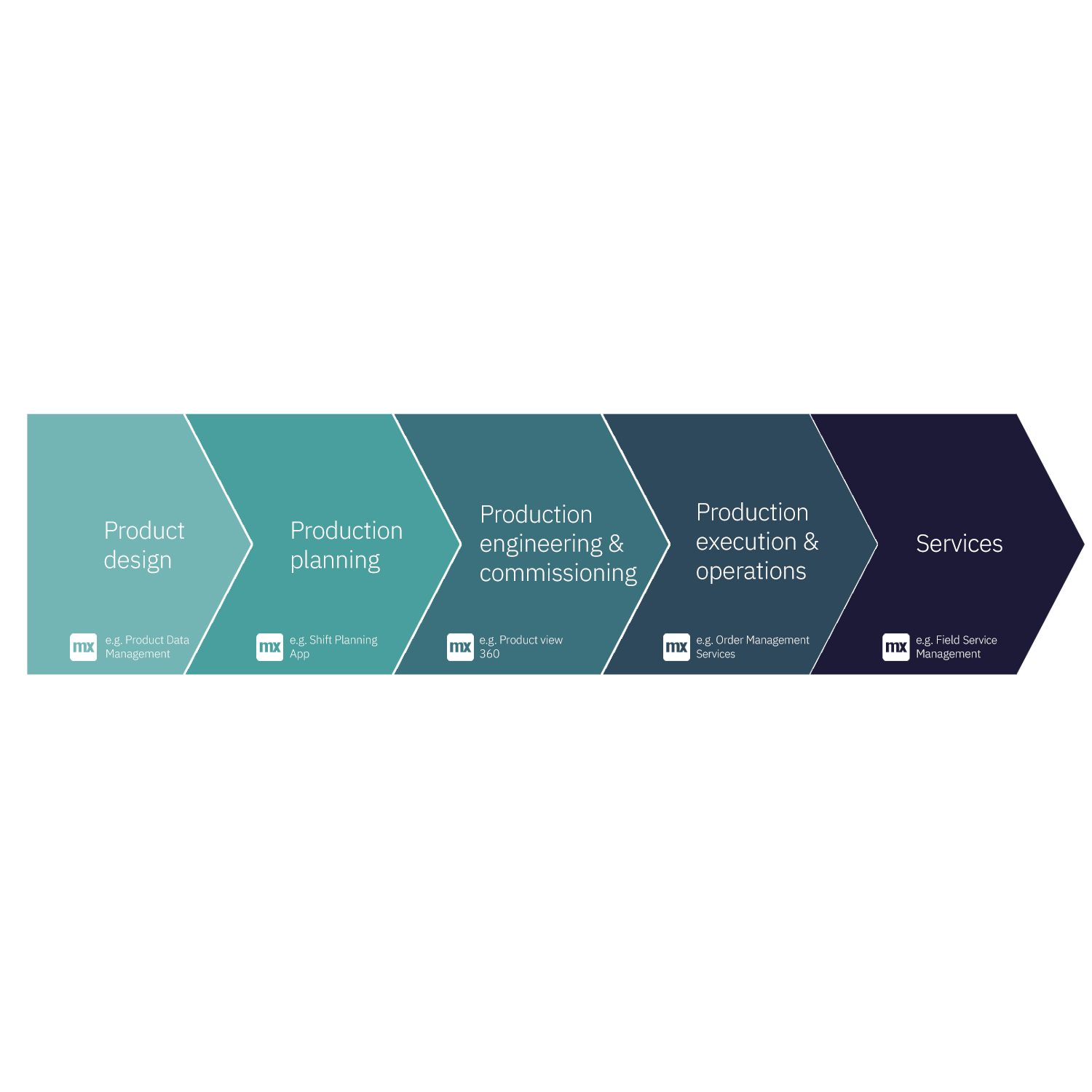
Supplier Management
With a good supplier portal you streamline and optimize the supply and distribution of raw materials, materials and products.
Warehousing & Logistics
Smart warehousing applications improve processes in the warehouse.
Marketing & Sales
With a good dealer portal with CPQ, customers can more easily generate leads and transfer orders to the production floor.
Safety, Health & Environment
Applications for more accurate quality control and a safety compass give you the opportunity to check all processes in the production process for safety.
Quality
Ensure that every safety protocol is not just recorded but followed diligently, reducing the risk of incidents and ensuring strict compliance.
Utilization & Performance
Examples of this aspect of manufacturing are tools and systems that help production companies to improve the occupancy rate and performance of a location.
Finance, Control & Reporting
This includes solutions that focus entirely on budget management and providing insight into operational costs and business results.
HR
The manufacturing menu of Emixa and Mendix houses all kinds of HR solutions, such as applications for employee communication and tools for scheduling and onboarding employees.
IT, Data & Facilities
In this area, our offering consists of a variety of supporting apps (applications to reserve rooms or register visitors) and solutions aimed at data enrichment activities.
With a good supplier portal you streamline and optimize the supply and distribution of raw materials, materials and products.
Smart warehousing applications improve processes in the warehouse.
With a good dealer portal with CPQ, customers can more easily generate leads and transfer orders to the production floor.
Applications for more accurate quality control and a safety compass give you the opportunity to check all processes in the production process for safety.
Examples of this aspect of manufacturing are tools and systems that help production companies to improve the occupancy rate and performance of a location.
This includes solutions that focus entirely on budget management and providing insight into operational costs and business results.
The manufacturing menu of Emixa and Mendix houses all kinds of HR solutions, such as applications for employee communication and tools for scheduling and onboarding employees.
In this area, our offering consists of a variety of supporting apps (applications to reserve rooms or register visitors) and solutions aimed at data enrichment activities.
Industry-specific Production Processes
Our solution, based on industry-specific production processes, offers added value at every stage of your production process.
Starting with product design, where we provide targeted solutions for product data management, making it easier to centrally capture product information, implement standardisation and manage revisions. This results in high-quality products that closely match the needs and preferences of your customers.
Our solution makes it possible to create shift schedules with specific applications that are perfectly tailored to this, creating efficient production schedules.
In product engineering and commissioning we bring together information from various sources, creating a complete picture of your production environment, business processes and product offering.
In the execution and operational phase, special applications and systems for order management are used to streamline production and ordering processes, as well as optimise inventory management.
Our services include on-site field service applications and support to customers after products are sold and out the door.
Industry-specific Production Processes
Our solution, based on industry-specific production processes, offers added value at every stage of your production process.
Starting with product design, where we provide targeted solutions for product data management, making it easier to centrally capture product information, implement standardisation and manage revisions. This results in high-quality products that closely match the needs and preferences of your customers.
Our solution makes it possible to create shift schedules with specific applications that are perfectly tailored to this, creating efficient production schedules.
In product engineering and commissioning we bring together information from various sources, creating a complete picture of your production environment, business processes and product offering.
In the execution and operational phase, special applications and systems for order management are used to streamline production and ordering processes, as well as optimise inventory management.
Our services include on-site field service applications and support to customers after products are sold and out the door.
A Selection from the Menu
.jpg)
Supplier Portal
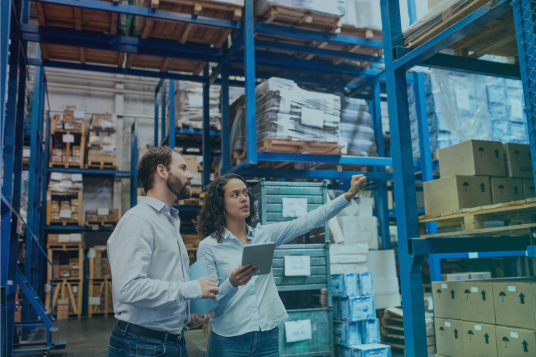
Smart Warehousing
.png)
Dealer Portal
.jpg)
Safety, Health & Environment
.jpg)
Quality Inspection
.png)
Utilization and Performance
.png)
Smart Financial Management
.png)
Human Resources
.png)
Data & Facilities
BOM Comparison
NTS, a leader in (opto)mechatronic systems for OEMs, faced a critical challenge: misalignment between their Bill of Materials (BoM) in Teamcenter and parts procurement in Navision. This led to discrepancies and manual cross-referencing, consuming up to a day of an engineer's time.
The solution was a Mendix app seamlessly integrated with Teamcenter and Navision. This app not only compared BoM structures but generated insightful reports on data governance and inconsistencies. Engineers used the first report to link incorrect parts between Navision and Teamcenter. Other reports streamlined the creation of new parts and BoM adjustments in Navision.
The impact was remarkable. What once took up to 50 days for an engineer was now accomplished in just one. Manual errors were minimized, and efficiency soared.
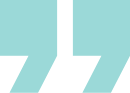
%2015%25%20(17).jpg)
Mendix app seamlessly integrated with Teamcenter and Navision.
Elevate your Industry with Emixa: Our Unique Advantages
Unlock Latent Value
Liberate and integrate isolated data within systems, facilitating seamless knowledge sharing.
Connected Ecosystems
To enhance operational efficiency, make supply chains and logistics more predictably streamlined.
Become Data-driven
Easy to use, people-oriented applications and workflows, driven by data.
Exceptional Experiences
Offering MTO and/or CTO products to effectively unburden the customer.
Time to Value
Providing comprehensive templates and solutions for generating ideas and facilitating rapid development.
Industry 4.0
Empower and modernize production with proven, innovative solutions.
Providing comprehensive templates and solutions for generating ideas and facilitating rapid development.
Low-code Turns Manufacturing Industry Upside Down
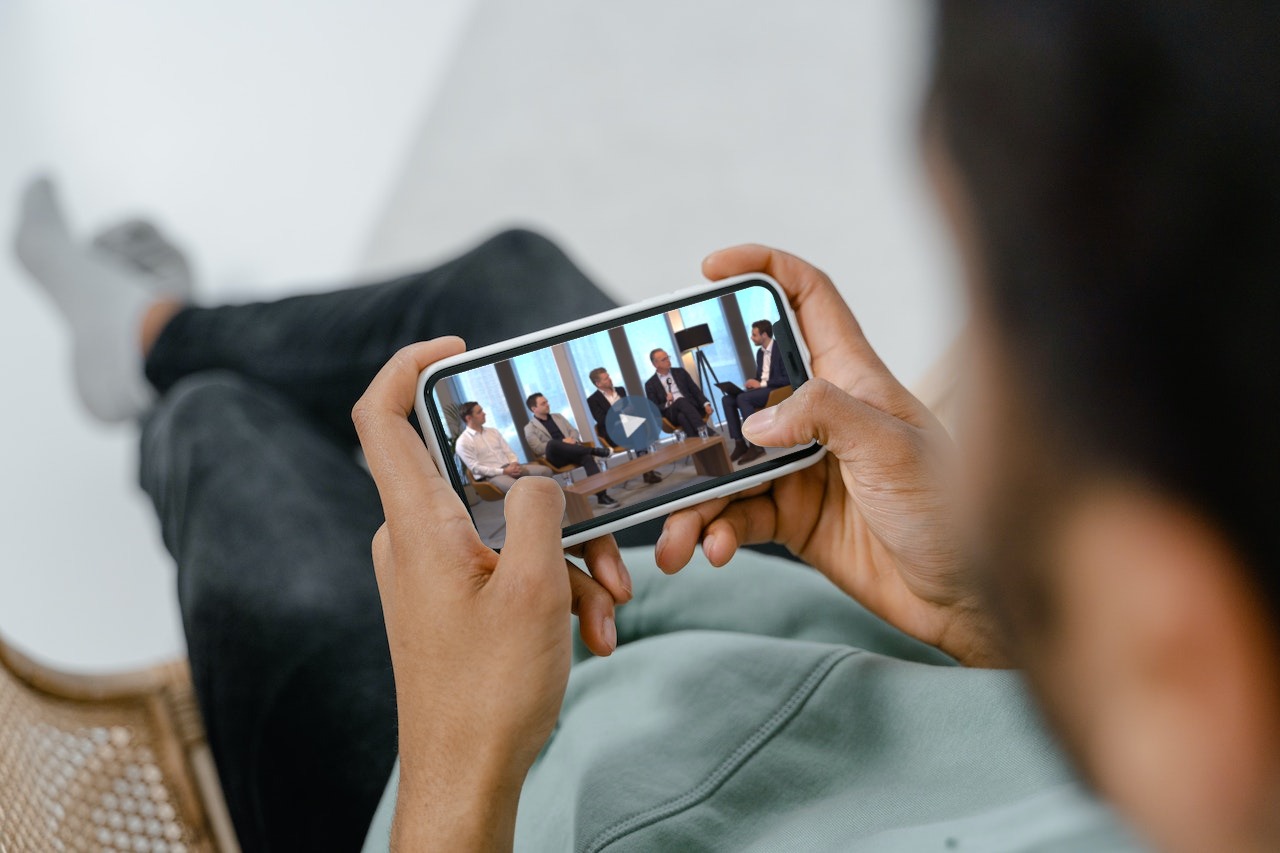
Leading Brands Trust Emixa's Expertise
At Emixa, we take pride in our collaborative journey with industry giants. These esteemed clients have entrusted us with their vision and challenges, and together, we've achieved remarkable success.
VIEW ALL CASES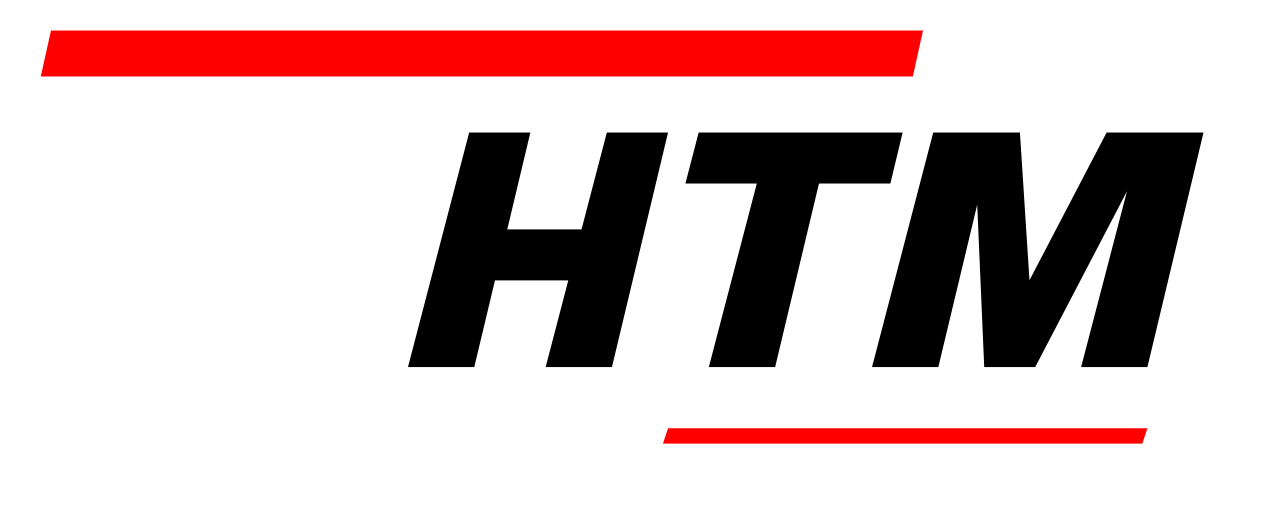
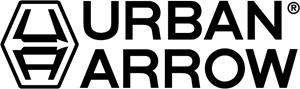
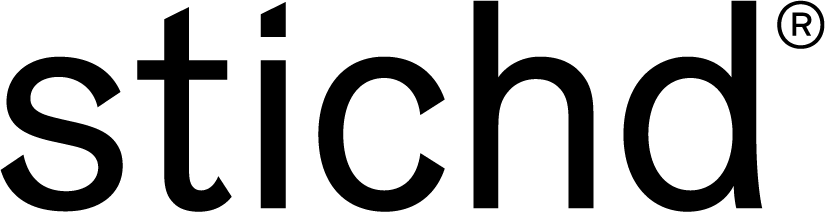
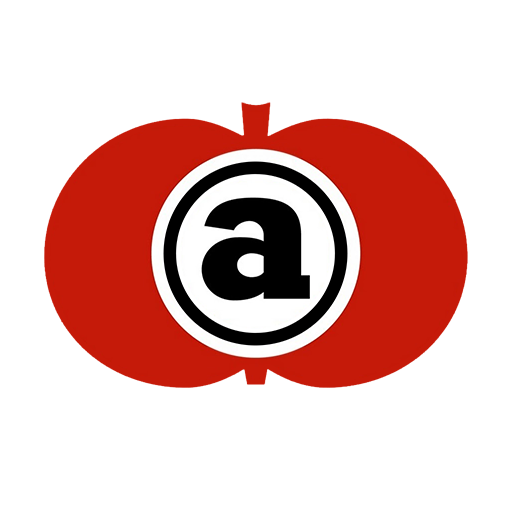
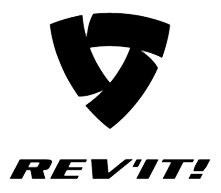
Frequently Asked Questions
Unlock Manufacturing Excellence
Want to learn more? Contact us for targeted applications in manufacturing.